Research Article
Volume 1 Issue 2 - 2019
Foamability and Foam Stability of Several Surfactants Solutions: The Role of Salinity and Oil Presence
Petroleum and Natural Gas Engineering Dept., College of Engineering, King Saud University, P.O. Box 800, Riyadh 11421, Saudi Arabia
*Corresponding Author: El-Mahdy Osama A, Petroleum and Natural Gas Engineering Dept., College of Engineering, King Saud University, P.O. Box 800, Riyadh 11421, Saudi Arabia.
Received: November 11, 2019; Published: November 21, 2019
Abstract
Foamability and foam stability are of main concerns in foam displacement for enhanced oil recovery. This work presents the output of systematic laboratory screening of foam ability and foam Stability of several surfactants. The surfactants examined were Brij 700, Triton X-100, Triton X-405, Zonyl FSO, Hitenol H-10, Hitenol H-20, Noigen N-10 and Noigen N-20. Solution salinity and oil presence effects were explored. Foam was generated by sparging Carbon Dioxide gas at a fixed flow rate through surfactants solutions and R5 parameter as suggested by Lunkenheimera and Malysa (2003) were used for foam stability testing. The results indicate the foam ability of all surfactants except for Triton X-405. Zonyl FSO and Hitenol H-10 were superior in term of foam stability with more stability as surfactants concentration increases. Equivalent optimum foam volumes were obtained for both surfactants but at higher concentrations of Hitenol H-10. Increasing solution salinity from 4% to 10% affected the foam stability negatively for low concentration solutions of Zonyl FSO but had no effect on foam stability of Hitenol H-10 solutions.
Foam stability and oil displacement efficiency were tested with different concentrations of Zonyl FSO and Hitenol H-10 solutions at 4% salinity. The presence of oil at the volume fraction implemented, affect the stability of the foam columns. The effect depends on the surfactant-type and surfactants concentrations where stability decreases at low Zonyl FSO concentration range and at all concentrations range tested of Hitenol H-10. In case of Zonyl FSO observations indicate that oil stayed in the lamellas skeleton and plateau boarders with no drain out. To the contrary, Hitenol H-10 was able to lift good portion of the oil column but oil was drained out of the foam structure within a short period of time.
Introduction
The declining trend of new discoveries coupled with the high demand for energy, directed the industry to the importance of enhanced oil recovery (EOR) processes in low recovery efficiency reservoirs. Gas flooding is a common mean of improving oil recovery. Gases have high mobility due to their low viscosity and density compared to reservoir fluids. This can cause gas to bypass and override the resident oil leading to inefficient sweep. Foam injection was first introduced by Bond and Holbrook (1958). It was suggested to overcome the high mobility associated with gas drive and to improve contact between oil and the injected gases. Later, Fried (1961) proved that foam can act as a gas-blocking agent.
Foams are usually formed in systematic hexagonal texture due gas dispersion through a continuous surfactant solution (Schramm and Wassmuth, 1994). This can be either by alternating injection or co-injection of gas and surfactant solution. Foam is thermodynamically unstable, and stability of the thin liquid films are important for foam stability and they are stabilized by surfactants to prevent bubble coalescence.
Foams are generally described in terms of their foamability defined as the capacity of the surfactants to form foam irrespective of the special foam properties and foam stability describing the variations of foam height or volume with time, immediately after foam generation (Malysa and Lunkenheimer, 2007). The two terms are interrelated and the more stable the foam films the greater is the solution's foamability.
Foam stability is dependent on electric double-layer repulsion (Israelachvili, 1991, Schramm and Wassmuth, 1994), gravity drainage, capillary suction, surface elasticity, dispersion force attraction, and steric repulsion and surface and bulk viscosity (Schramm and Wassmuth, 1994). An increased surface and bulk viscosity do not contribute directly to film stabilization. They rather act as resistances to the film thinning and rupturing processes.
Foam generation generally increases with increasing surfactant concentration up to the critical micelle concentration (CMC) above which surfactant concentration has little effect (Chiang et al., 1980). Marsden and Khan (1966) found that the apparent viscosity increases with increasing surfactant concentration.
Foam stability in presence of oil is related to foam-oil interaction. Literatures indicated the role of oil presence on foam stability (Aveyard et al., 1994; Denkov, 1999; Bergeron et al., 1993; Schramm, 1994; Garrett, 1993). Wasan et al. (1994) indicated that foam stability in presence of oil is related to pseudo emulsion film between oil drops and gas. Vikingstad et al. (2005) performed static foam tests and observed that foam stability in presence of oil is related to foam transport properties affected by surfactant ability to solubilize oil molecules. Oils characterized with higher molecular weight can stabilize the generated foam compared to lower molecular weight oils.
Three major mechanisms have been considered for the antifoaming property of the dispersed oils. These are aqueous film thinning rate during oil entry, oil spreading on the water surface, and thin water film bridging (Nikolov et al., 1986; Lau, and O’Brien, 1988). Simjoo et al. (2013) suggested that foam decay in presence of oil starts as small and rapid decay dominated by gravity drainage, followed by a stabilized foam volume, and then a second continuous decay due to bubble coalescence over a relatively long time. The oil foam destabilization is more pronounced for oils with a smaller molecular weight. Farajzadeh et al. (2010) showed that CO2 injection below the gas minimum miscibility pressure hardly foams in the oil-bearing section of the porous medium.
Vikingstad et al. (2005) indicated that surfactant solution salinity is a main factor affecting foam stability and this effect is more pronounced in presence of oil. Their work showed that low salinity solutions can generate more stable foam than high salinity ones. Aronson et al (1994) indicated that stability ensured by a disjoining pressure in the lamella between two foam bubbles is directly dependent on the concentration of surfactants and salt that are used in foam flooding in porous media.
In this work we investigated the foam ability and foam stability of several surfactants. Measurements were made at different surfactant concentrations at different solution salinities in presence and absence of crude oil.
Experimental Procedure
The application of the t1/2 parameter for metastable foams comparison can be time consuming. Lunkenheimera and Malysa (2003) proposed a parameter called R5 to examine the foam stability of the surfactant solutions. This parameter is determined as the ratio of the foam height at five minutes after foaming (h5) to the initial formed foam height (h0). According to their investigation, foams with R5 of 50% can be considered as metastable, whereas lower values of R5 indicate foams of low stability.
The application of the t1/2 parameter for metastable foams comparison can be time consuming. Lunkenheimera and Malysa (2003) proposed a parameter called R5 to examine the foam stability of the surfactant solutions. This parameter is determined as the ratio of the foam height at five minutes after foaming (h5) to the initial formed foam height (h0). According to their investigation, foams with R5 of 50% can be considered as metastable, whereas lower values of R5 indicate foams of low stability.
The apparatus used is simple setup shown in (Figure 1). It consists of a glass column 100 cm long and 1.6 cm inner diameter equipped with glass frit placed at the base of the column. Foam was generated by injecting gas into the solution using a syringe for gas supply. The experiments are conducted by slowly pouring surfactant solution (12.5 mL) into the glass column. Carbon Dioxide gas (50 mL) is introduced into solution manually using syringe within a period of 20 seconds. After gas introduction, the stopcock connecting the column with the syringe is immediately closed, and the initial foam and solution heights are measured. Foam height and solution level are then measured at five minutes in order to determine the R5 parameter.
The foaming in presence of oil is investigated by adding oil to the surfactant solution before gas injection. The amount of oil was calculated as a volume fraction of the surfactant solution and 5.0 % by volume is poured into the column. All measurements were repeated 2 to 3 times for every solution concentration at ambient temperature and atmospheric pressure.
Materials
Several surfactants were investigated. These surfactants are nonionic (Brij 700, Triton X-100, Triton X-405, and Zonyl FSO, Noigen N-10 and Noigen N-20), anionic (Hitenol H-10, Hitenol H-20). Surfactant solutions of different concentrations were prepared by diluting them in brines of 4% and 10% salinities. Table 1 and 2 list the compositions of brine solutions. Oleic phase were medium to heavy crude oil (23 API, 90 cp). High purity Carbon Dioxide gas was used to generate the foam.
Component | Weight* (g) | Weight (%) |
NaCl | 61.26 | 3.06 |
KCl | 0.58 | 0.029 |
CaCl2 | 10.86 | 0.54 |
MgCl2.6H2O | 5.19 | 0.26 |
Na2SO4 | 5.91 | 0.30 |
H2O | 1916.20 | 95.81 |
*Based on 2000 g brine solution |
Table 1: Composition of 4.19% brine.
Component | Weight* (g) | Weight (%) |
NaCl | 57.235 | 5.7235 |
CaCl2 | 35.82 | 3.582 |
MgCl2.6H2O | 7.261 | 0.7261 |
H2O | 899.684 | 89.9684 |
*Based on 1000 g brine solution |
Table 2: Composition of 10% brine.
Results and Discussion
To investigate the foam stability during the foam formation, each surfactant concentration was introduced with gas volumes of 25 and 50 cc during time period of 20 seconds. This corresponds to average volumetric rates of 4.5 and 9 L/hr. Figure 2 is an example plot of initial foam height of Hitenol H-10 surfactant solutions as a function of surfactant concentration. The figure shows a two times greater foam height when gas injection was doubled from 4.5 L/hr to 9 L/hr indicating an initial foam volume equivalent to the dispersed gas and solution volumes lifted by the foam generated. Hence, a stable foam structure was formed with no significant rupture. Figure 3 summarizes the results for all surfactants solution investigated. All can be described with good foam ability during foam column formation except for Triton X-405 where foam height was increased by only 50% when gas rate of injection was doubled.
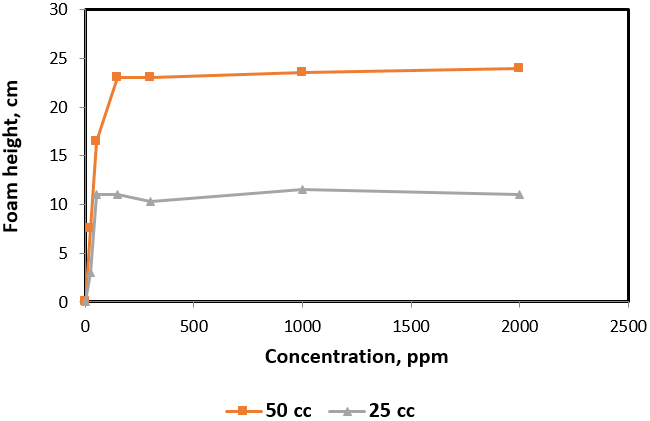
Figure 2: Foam height versus surfactant concentration of 4% salinity Hitenol H10 solutions at 25 and 50 cc of gas injection.
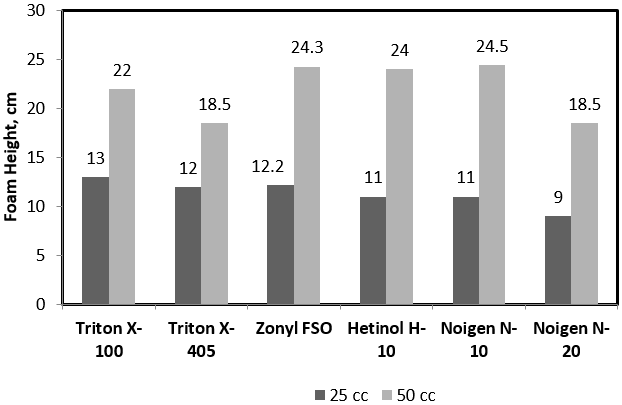
Figure 3: Foam height versus surfactant concentration of 4% salinity surfactant solutions at 25 and 50 cc of gas injection.
The half time decay (t1/2) of foam column is the most common method used to test foam stability. As indicated earlier this method can be time consuming, hence R5 method was used for quick evaluation of foam stability. Figure 4 plots the R5 values as a function of surfactants concentrations for all surfactants solutions. Except for the Zonyl FSO and Hitenol H-10, all tested surfactants solutions are characterized poor stability foamers with full foams rupture at a very short time frame of less than 5 minutes. Zonyl FSO provided a constant R5 value of 65% at 200 ppm surfactant concentrations and above. Hitenol H-10 surfactant solutions indicate a low R5 values below 50 ppm concentrations with a sharp increase in R5 between 50 ppm and 150 ppm and a constant R5 value around 60% above 150 ppm. Accordingly both surfactants are considered metastable as indicated by R5 values above 50% with transition from low stability to high stability within a range of surfactant concentrations. Zonyl FSO required a wider range of concentrations to reach stability compared to Hitenol H-10 and that can be related to the different surface activities of the two surfactants.
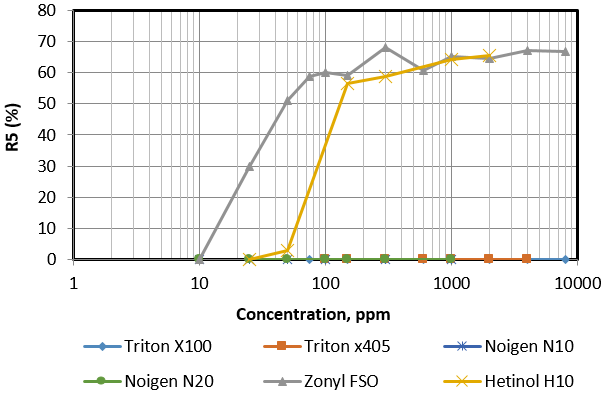
Figure 4: Variation of R5 as a function of surfactant concentration of different tested surfactants.
The effect of solution salinity on foam stability was tested by comparing the results of Zonyl FSO and Hitenol H-10 solutions at two different salinities of 4% and 10%. Figure 5 and 6 present the effect of salinity on R5 trend of Zonyl FSO and Hitenol H-10 surfactants solutions respectively. Figure 5 shows less foam stability at low concentrations of high salinity Zonyl FSO surfactant as indicated by the sharp increase of R5 values within a narrow range of concentrations (about 20 ppm) compared to a much wider range for low salinity solution. No effect was noticed at higher concentrations. Figure 6 on the other hand indicates a matching trend of R5 values at low and medium Hitenol H-10 concentrations with slight decrease of R5 values at higher concentrations, higher salinity Hitenol H-10 solutions.
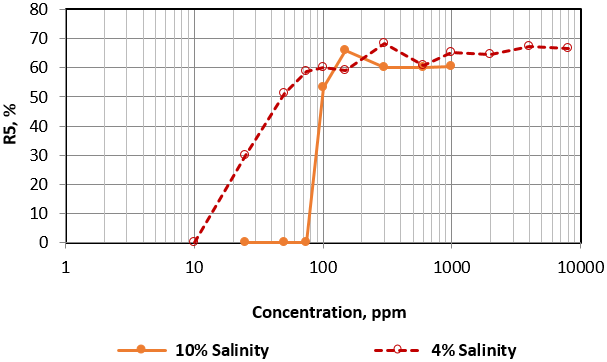
Figure 5: Variation of R5 as a function of surfactant concentration of Zonyl FSO at different solution salinities.
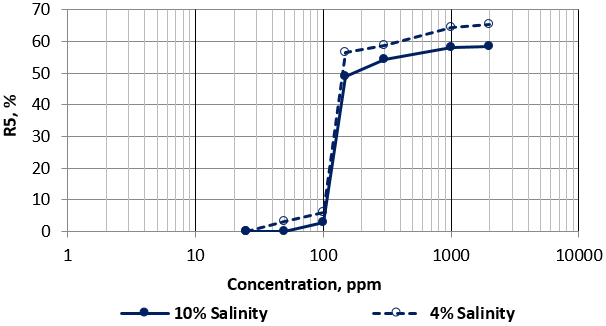
Figure 6: Variation of R5 as a function of surfactant concentration of Hitenol H10 at different solution salinities.
Figure 7 shows snapshots of the foam columns generated by low and high concentrations of Zonyl FSO and Hitenol H-10 both at 10% salinity. High concentration solutions were characterized by fine and fairly uniform distributed bubble size whereas lower concentrations clearly reveals a different foam texture with larger bubble sizes and broad distribution. These snapshots correlate well with the R5 tests shown in figure 5 and 6.
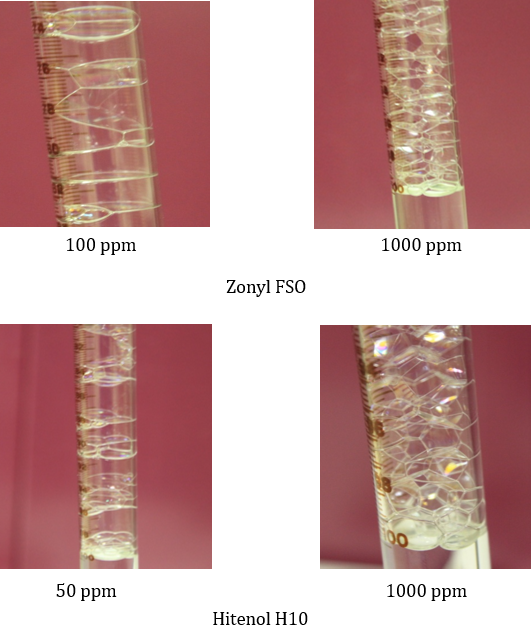
Figure 7: Foam structure of low and high concentrations of Zonyl FSO and Hitenol H10 at 10% salinity.
A major concern when applying foam for mobility control is its stability in the presence of oil. Foam stability of Zonyl FSO and Hitenol H-10 solutions at 4% salinity were tested in presence of medium to heavy crude oil and results obtained were compared with those obtained previously in absence of oil. Figures 8 and 9 compare the foam stability of Zonyl FSO and Hitenol H-10 respectively in presence and absence of oil. In presence of oil, Zonyl FSO solutions indicate lower foam height at lower concentrations (Figure 8). No effect was seen at concentrations above 100 ppm. Observation indicate a good foam height but with some gap in the lower portion of the foam column and low oil lift at concentrations on the range 100 to 300 ppm. Above 600 ppm a good foam structure was obtained with good stability and efficiency in lifting good portion of the oil at the lamellas skeleton and plateau boarders with no drainage as shown in Figure 10.
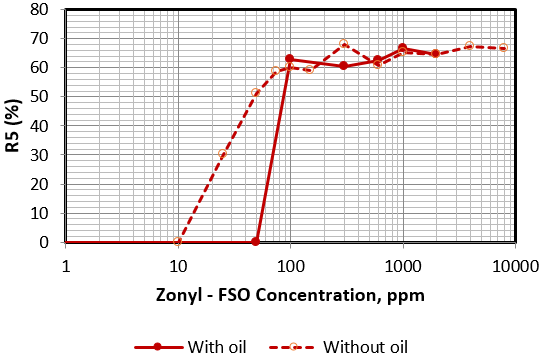
Figure 8: Variation of R5 as a function of surfactant concentration of Zonyl FSO in presence and absence of oil.
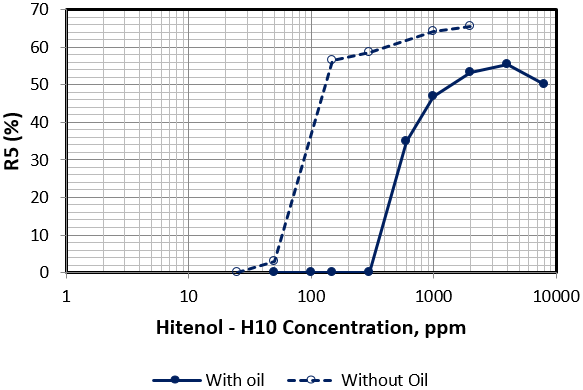
Figure 9: Variation of R5 as a function of surfactant concentration of Hitenol H-10 in presence and absence of oil.
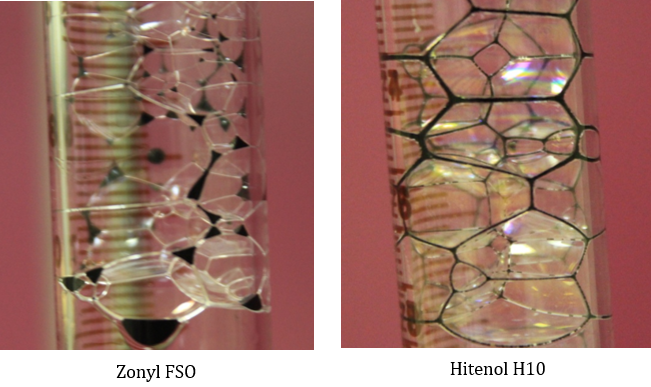
Figure 10: Effect of oil presence on foam structure and stability at 1000 ppm surfactant concentration diluted in 4% brine.
Figure 9 showed drastic lower foam height of Hitenol H-10 with very week stability in which foam vanishes as gas injection ceases at concentrations around 100 ppm. As concentration increases within the range of 150 to 300 ppm, good foam height was observed but with week structure in which foam vanishes completely within the first minute. As concentration increases above 1000 ppm we obtained a good foam height with reasonable stability and oil displacing efficiency. Figure 10 present a snapshot showing oil phase distribution inside the foam structure accumulating at the plateau borders indicating the strength of Hitenol H-10 foam films. However, lifted oil drained out of the foam structure within short time frame. Presence of oil, at the volume fraction implemented, affect the stability of the foam columns. The effect depends on the surfactant-type and surfactant concentration where stability decreases at low concentrations of Zonyl FSO and at all concentrations range tested of Hitenol H-10.
Conclusions
Foam ability and foam stability of several anionic and nonionic surfactants were investigated. Foam characteristics were studied at different solutions salinities in absence and presence of crude oil. The following are the main outcomes of the work:
- All surfactants except Triton X-405 showed good formability but Zonyl FSO and Hitenol H-10 surfactants provided the highest foam longevity in the absence of oil.
- Foamability and foam stability enhances as surfactants concentrations increases.
- High concentration solutions were characterized by fine and fairly uniform distributed bubble size whereas lower concentrations clearly reveals a different foam texture with larger bubble sizes and broad distribution.
- Higher salinity reduces the foam stability at low concentrations of Zonyl FSO surfactant. No effect was seen at higher concentrations. On the other hand, no effect was observed on foam stability of Hitenol H-10 solutions at different concentrations except for small drop on foam longevity at higher concentrations.
- In presence of oil, lower concentrations Zonyl FSO solutions provided lower foam stability. Foam stability was not affected at concentrations above 100 ppm. On the other hand, lower stability was noticed at all concentration range tested of Hitenol H-10.
- Hitenol H-10 surfactant was able to carry good portion of the oil upward but that oil drained out of the foam structure. To the contrary, Oil phase was distributed inside the foam structure of Zonyl FSO accumulating at the plateau borders indicating the strength of foam films.
References
- Bond, D. C. and Holbrook, O. C., U.S. Patent No. 2,866,507, 30th December 1958.
- Fried, A. N., (1961). The Foam Drive Processes for Increasing the Recovery of Oil, No. Report of Investigations 5866, USBM.
- Schramm, L. L., and Wassmuth, F., (1994). Foams: Basic Principles, In: Foams: Fundamentals & Applications in the Petroleum Industry, Schramm, L.L. (ed.), American Chemical Society, and Washington, DC.
- Malysa, K. and Lunkenheimer, K., (2008). Foams under dynamic conditions, Current Opinion in Colloid & Interface Science 13 pp. 150-162.
- Israelachvili, J. N., (1966). Intermolecular & Surface Forces, 2ed, Academic Press, San Diego, 1991. S. S. Marsden, Soc. Pet. Eng. J. 6, 17.
- Chiang, J. C., Sanyal, S. K., Castanier, L. M., Brigham, W. E., and Sufi, A., (1980). Foam as a Mobility Control Agent in steam Injection Processes, paper SPE 8912 presented at the 50th Annual California Regional Meeting, Los Angeles, April, 9-11.
- Marsden, S. S., and Khan, S. A., ((1966). The Flow of Foam Through Porous Media and Apparent Viscosity measurements, Soc. Pet. Eng. J., pp. 17-25,.
- Aveyard, R., Binks, B. P., Fletcher, P. D. I., Peck, T. G. and Garrett, P. R., (1993). Entry and spreading of alkane drops at the air-surfactant solution interface in relation to foam and soap film stability, J. Chem. Soc. Faraday Trans., 89 pp. 4313-4321.
- Denkov, N. D., Mechanisms of foam destruction by oil-based antifoams, Langmuir, 20 (2004), pp. 9463-9505.
- Bergeron, V., Fagan, M. E. and Radke, C. J., (1993). Generalized Entering Coefficients - A Criterion for Foam Stability against Oil in Porous Media, Langmuir 9 (7), pp. 1704-1713.
- Garrett, P. R., (1993). The mode of action of antifoams, In: Defoaming: theory and industrial applications; Garrett, P.R. (ed.), Marcel Dekker, New York.
- Wasan, D., Nikolov, A., Huang, D. and Edwards, D., (1988). Foam stability: effects of oil and film stratification, In: Surfactant-based mobility control progress in miscible-flood enhanced oil recovery, Smith, D.H. (ed.), American Chemical Society, Washington, DC.
- Vikingstad Anne Kari, Skauge A., Høiland H., Aarra M., (2005). Foam–oil interactions analyzed by static foam tests, Colloids and Surfaces A: Physicochem. Eng. Aspects 260, pp. 189-198.
- Nikolov, A. D., Wasan, D. T., Huang, D. W. and Edwards, D. A., (1986). The effect of oil on foam stability: mechanisms and implications for oil displacement by foam in porous media, Paper SPE15443-MS presented at The Annual Technical Conference and Exhibition, 5-8 October New Orleans, Louisiana.
- Lau, H. C. and O’Brien, S. M., (1988). Effects of spreading and non-spreading oils on foam propagation through porus media, SPE Reservoir Engineering, p. 893-896.
- Simjoo, M., Rezaei, T., Andrianov, A. and Zitha, P. L. J., (2013). Foam stability in the presence of oil: effect of surfactant concentration and oil type, Colloids and Surfaces A: Physicochem. Eng. Aspects, Accepted manuscript.
- Farajzadeh R., Wassing B. M. and Boerrigter P. M., (2012). Foam assisted gas–oil gravity drainage in naturally fractured reservoirs, Journal of Petroleum Science and Engineering, 94-95, pp. 112–122.
- Kuhlman, M. I., (1990). Visualizing the effect of light oil on CO2 foams, Journal of Petroleum Technology, 42 pp. 90-908.
- Aronson, A. S., Bergeron, V., Fagan, M. E., and Radke, C. J., (1994). The Influence of Disjoining Pressure on Foam Stability and Flow in Porous Media, Colloids and Surfaces A. 83, pp. 109-120.
Citation: El-Mahdy Osama A. (2019). Foamability and Foam Stability of Several Surfactants Solutions: The Role of Salinity and Oil Presence. Archives of Chemistry and Chemical Engineering 1(2).
Copyright: © 2019 El-Mahdy Osama A. This is an open-access article distributed under the terms of the Creative Commons Attribution License, which permits unrestricted use, distribution, and reproduction in any medium, provided the original author and source are credited.