Research Article
Volume 1 Issue 1 - 2019
Development, Characterization and Tribological Behavior of ASTM Grade Commercial Steel Reinforced with Tungsten Carbide (WC) Metallic Chilled Composites for Stone Crusher Jaw Application.
Professor & Associate Dean, School of Engineering, Presidency University, Bangalore, India
*Corresponding Author: Joel Hemanth, Professor & Associate Dean, School of Engineering, Presidency University, Bangalore, India.
Received: October 17, 2019; Published: October 28, 2019
Abstract
Present research deals with the production of metallic chilled ASTM A216 WCB steel (plane carbon group) having 0.5% chromium reinforced with tungsten carbide (WC) particles (3 to 15 wt.% in steps of 3 wt.%) to study the effect of copper chilling on microstructure, mechanical properties and wear behavior. The specimens taken from the chilled casting blocks were tested for their strength, hardness and wear behavior. Results of microstructural studies indicate that the chilled castings were sound with refined grain particles (effect of chilling) distributed evenly with good bonding in the matrix. It was found from the present investigation that chilling effect that produces hard carbide formation in steel as well as directional solidification and addition of the reinforcement in steps has improved both mechanical properties (strength and hardness) and wear resistance of the steel composite developed. It is concluded from the above investigation that chilling during solidification and reinforcement content has the increased the strength by 35%, hardness by 23% and high wear resistance with high coefficient of friction as compared against the matrix alloy. It is concluded that increase in mechanical properties and wear resistance are due to incorporation of WC particles and effect of chilling.
Keywords: Composite; Strength; Hardness; Chill; Steel and wear
Introduction
Iron is abundantly found in the earth’s crest and it do not possess the desired mechanical properties for engineering application. Steel which is an alloy of iron and carbon is known for its strength, hardness, weldment and hence it is most fit for many engineering applications viz. automobile, marine, structural etc. The combination of strength and ductility adds to give steel greater values of toughness and resistance to shock. It is well known that, properties of steel can be controlled by controlling its composition or by heat treatment.
Systematic study of literature review indicate that steel belongs to Old Stone Age era and later finds its extensive development and use after industrial revolution. During 19th and beginning of 20th century research on steel was mainly focused on alloying and heat treatment. But a notable development has taken place during the end of 20th century where steel composites came into existence where the researchers around the world focused on developing lighter and stronger material. Later in the 21st century notable development has taken place due to the fact that MMCs has firmly made their mark in various applications including welding of composites. Hence the research is going on still developing the next generation MMCs by reinforcing hard ceramic particles in the steel matrix.
Composite materials are the class of materials in which two phases are combined usually with strong interfaces between them. To improve the mechanical properties especially the hardness, strength and wear resistance and also to reduce the weight, composites came into existence. Now a days such steel composites are developed for marine, rollers, crusher’s jaws, rail car wheels and structural applications. The main focus involved in fabricating the chilled steel Metal Matrix Composite (MMC) in the present research is to combine the desirable properties of steel (matrix material), effect of chilling to produce pearlite matrix with carbides, directional solidification to avoid micro porosity and the effect of reinforcement of tungsten carbide. Addition of reinforcement particle which has very high strength and hardness converts a plane carbon steel to a pearlitic structured steel that results in a composite whose mechanical properties wear behavior are superior compared with un-reinforced steel.
In a study on effect of high rate heat transfer during solidification of alloyed cast iron using water-cooled and sub-zero chills on mechanical behavior [1] concluded that number of eutectic cells is significantly larger in the case of chilled cast iron than that obtained in the case of cast iron cast without a chill. Eutectic cell count was shown to be a major factor that affects ultimate tensile strength and fracture toughness. In another study on microstructure of cryogenically treated M2 tool steel [2] it is reported that, cryogenic treatment facilitate the formation of carbon clustering and increase the carbon density in the subsequent heat treatment improves the wear resistance of steel.
Collins and Dormer [3] has studied the effect of Deep Cryogenically Treated (DCT) on D2 cold work tool steel and found that, DCT steels give lowest wear rate compared to conventionally heat treated steels. Barron [4] conducted some preliminary tests to determine the effect of cryogenic treatment on lathe tools, end mills and found that an increase in tool life from 25% to 35% was observed for the tools which have been soaked in liquid nitrogen for 12 hours. Meng and Tagashira [5] have studied the wear resistance of Fe-12Cr-Mo-V-1.4C tool steel both with and without cryogenic treatment. The study reveals that conventionally heat treated and cryogenically treated specimens showed smaller wear volume at all sliding distances. Bensely et al., [6] made comparative study on wear resistance improvement through DCT and Shallow Cryogenic Treatment (SCT) using pin-on-disc wear tester. Although the hardness value between the SCT and DCT samples are the same, wear resistance of DCT samples are high compared with SCT samples, which is due to precipitation and finer distribution of carbides. In a study on wear and corrosion wear of medium carbon steel it was found that, the samples showed smaller weight loss and lower friction co-efficient in the presence of corrosive environment [7]. In an investigation it was found that wear resistance improved dramatically through thermo-mechanical treatment due to elimination of porosity [8]. In another research it was demonstrated that wear rate was largest in the as cast form having highest weight loss [9].
The main intention in fabricating the chilled steel composite to make a tailor made material that has an excellent strength to weight ratio that attracts many practical applications where fuel consumption is to be reduces with enhancement in mechanical properties. Driven by the ever increasing demand for strength, hardness and wear resistance, commercial steel can be reinforced on weight adjustment basis to outperform the conventional material.
Hence in the present investigation, reinforcement addition and chilling during solidification was adopted to eliminate micro-porosity, to improve mechanical properties and wear behavior of the steel composite developed [10, 11]. Chill method of casting is used in the present investigation since chill extracts heat at faster rate and promotes directional solidification. Heat extraction from steel castings makes the steel structure fine pearlite (desired steel structure) with more carbide formation. Further, addition of reinforcement to such chilled steel structure further enhances the properties. Search of open literature indicates that so for no investigation has been reported on mechanical properties and wear behavior of chilled steel reinforced with WC particles. Present research is a healthy way to convert a low grade steel to a superior engineering material ie., chilled steel composite that finds extensive use in rollers, crusher jaws, rail car wheels etc.
Relevance of the Present Research
The objective of present research is to examine the effect of addition of tungsten carbide (WC) on the microstructure, mechanical properties and wear behavior of copper chilled ASTM A216 WCB steel which belong to plain carbon group. These steels are widely used in the production of valves, flanges, motor casing, rollers for crushing ores and fittings at high temperature service. In the present investigation effort has been made to enhance the mechanical properties using a different route by adding reinforcement and chilling effect during solidification. The resulting chilled steel composite was fabricated in the form of crusher jaws (rectangular shape) for stone crushing machines.
The objective of present research is to examine the effect of addition of tungsten carbide (WC) on the microstructure, mechanical properties and wear behavior of copper chilled ASTM A216 WCB steel which belong to plain carbon group. These steels are widely used in the production of valves, flanges, motor casing, rollers for crushing ores and fittings at high temperature service. In the present investigation effort has been made to enhance the mechanical properties using a different route by adding reinforcement and chilling effect during solidification. The resulting chilled steel composite was fabricated in the form of crusher jaws (rectangular shape) for stone crushing machines.
Experimental Procedure
Molding, Melting and Composite Making.
Commercial grade steel having standard composition (ASTM A216 WCB grade) was selected which is of importance in automotive and structural applications has made the most suitable matrix material of the present research. Tungsten carbide was selected as the reinforcement because of its excellent mechanical and thermal properties and it availability in powder form. Table 1 and 2 shows the composition and properties of both the matrix and the reinforcement.
Molding, Melting and Composite Making.
Commercial grade steel having standard composition (ASTM A216 WCB grade) was selected which is of importance in automotive and structural applications has made the most suitable matrix material of the present research. Tungsten carbide was selected as the reinforcement because of its excellent mechanical and thermal properties and it availability in powder form. Table 1 and 2 shows the composition and properties of both the matrix and the reinforcement.
In the present research metallic chill ie, copper chill blocks were used to get test castings. The reason for using copper chills is because of its high VHC (Volumetric Heat Capacity), availability and fabrication. These chill blocks were fabricated to required size and set in CO2 sand molds of size 750 *450*100 mm rectangular block which is the standard jaw size of stone crushing machine. Zircon sand coating was applied to mold to get good surface finish as well to avoid fusing of sand.
Steel alloy having the composition of ASTM A216, WCB grade with 0.5% Cr addition was melted in an induction furnace attached with a stirrer. The melt was superheated to 1640ºC and was taken into a preheated ladle containing calcium silicide (deoxidizing agent) during pouring. Finally, tungsten carbide reinforcement (100 to 150 µm size) was added in steps of 3 to 15 wt.% in steps of 3 wt.% to the treated molten metal and stirred well with stirrer attached to the composite making furnace slowly at a speed of 200 rpm and finally poured into the mold (at 1625ºC) containing copper end chills set in the mold. After solidification, all the test castings (chilled steel composite) were cleaned and heat treated (annealing) and from this the specimens were taken from the chilled face for various tests.
Element C Si Mn P S Cr Mo Ni Fe |
Comp. 0.235 0.351 0.994 0.034 0.012 0.234 < 0.001 0.014 Bal |
(Comp: Composition)
Table 1: Chemical composition (wt.%) of ASTM A216, WCB steel.
Table 1: Chemical composition (wt.%) of ASTM A216, WCB steel.
Properties MP (°C) TC (w/mk) Density (gm.cc) Crystal |
2870 110 15.63 Hexagonal |
(MP: Melting point, TC: Thermal conductivity)
Table 2: Properties of Tungsten Carbide (WC).
Table 2: Properties of Tungsten Carbide (WC).
Testing.
Metallographic Examination.
The specimens for micro structural studies were polished according to metallurgical standards and fine polishing was done using alumina powder and diamond paste. The specimens were etched with 3% Nital to evolve grain boundaries. Micro- structural studies were done using Olympus optical metallurgical microscope with CEMEX image analyzer according to ASTM 3 standards. SEM was used to study the wear surface and wear morphology of the worn surface. XRD analysis was also carried out on the composite developed to confirm the presence of reinforcement and formation of any other secondary phases.
Metallographic Examination.
The specimens for micro structural studies were polished according to metallurgical standards and fine polishing was done using alumina powder and diamond paste. The specimens were etched with 3% Nital to evolve grain boundaries. Micro- structural studies were done using Olympus optical metallurgical microscope with CEMEX image analyzer according to ASTM 3 standards. SEM was used to study the wear surface and wear morphology of the worn surface. XRD analysis was also carried out on the composite developed to confirm the presence of reinforcement and formation of any other secondary phases.
Tensile and Hardness tests
The specimens for mechanical tests were taken from the chill end of the casting and were prepared according to ASTM standards. Tension tests on a tensometer specimens were conducted at ambient temperature on Instron universal tension testing machine of 60 ton capacity in the load range of 0–2000 kN according to ASTM –E 8M standards. Rockwell hardness (HRC) for the samples was measured using ZWICK-Roll ZHR hardness tester with a load of 100 kg-f using ball indenter of size 1/16 inch in diameter. Polished specimens used for microstructural examination was used for the hardness measurements.
The specimens for mechanical tests were taken from the chill end of the casting and were prepared according to ASTM standards. Tension tests on a tensometer specimens were conducted at ambient temperature on Instron universal tension testing machine of 60 ton capacity in the load range of 0–2000 kN according to ASTM –E 8M standards. Rockwell hardness (HRC) for the samples was measured using ZWICK-Roll ZHR hardness tester with a load of 100 kg-f using ball indenter of size 1/16 inch in diameter. Polished specimens used for microstructural examination was used for the hardness measurements.
Sliding wear test
Wear test for the samples are conducted using pin on disc computerized DUCOM make wear testing machine according to ASTM G99-17 standard. The specimen is a pin of size 6 mm in diameter and 25 mm long whereas the disc is of alloy steel having hardness of HRC 200. Before the test, the surface of the pin was cleaned with acetone and volume loss method (LVDT attached to the specimen to measure change in length) was adopted in the present investigation. Test was carried out by applying normal load on pin from 20 to 60 N in steps of 20 N at different disc speeds. Note that the results reported for various tests are the average of three repetitions of the same sample at the same location.
Wear test for the samples are conducted using pin on disc computerized DUCOM make wear testing machine according to ASTM G99-17 standard. The specimen is a pin of size 6 mm in diameter and 25 mm long whereas the disc is of alloy steel having hardness of HRC 200. Before the test, the surface of the pin was cleaned with acetone and volume loss method (LVDT attached to the specimen to measure change in length) was adopted in the present investigation. Test was carried out by applying normal load on pin from 20 to 60 N in steps of 20 N at different disc speeds. Note that the results reported for various tests are the average of three repetitions of the same sample at the same location.
Results and Discussions.
Solidification of the Composite.
Figure 2 (a to d) shows microstructure of steel composite having different wt.% addition of reinforcement (6, 9, 12 and 15 wt.%), cast using copper chill, Figure 2 (e and h) shows eutectic cell count (at low magnification at 50 X) and figure 2 (i and l) shows Dendrite Arm Spacing (DAS). The differences in associated graphite, its randomness, length and its matrix structure (as shown in figure 2, a to d) for the various specimens cast were analyzed and correlated to its mechanical properties. Faster the cooling rate (chilling) produces fine, highly oriented dendrites, while slow cooling (un-chilled) produces large, coarse dendrites. Therefore, solidification over a temperature range is the primary requirement for dendrite growth. Primary austenite dendrites readily grow from the liquidus down to the eutectic temperature and growth of dendrites may also continue concurrently with the eutectic as the temperature decreases through eutectic range to the solidus. Thus, under cooling in case of chilled steel may lead to smaller dendrites and higher interaction. Hence, the eutectic cells solidify around these austenite dendrites and in this manner the entire microstructure is affected by the number and size of the dendrites.
Figure 2 (a to d) shows microstructure of steel composite having different wt.% addition of reinforcement (6, 9, 12 and 15 wt.%), cast using copper chill, Figure 2 (e and h) shows eutectic cell count (at low magnification at 50 X) and figure 2 (i and l) shows Dendrite Arm Spacing (DAS). The differences in associated graphite, its randomness, length and its matrix structure (as shown in figure 2, a to d) for the various specimens cast were analyzed and correlated to its mechanical properties. Faster the cooling rate (chilling) produces fine, highly oriented dendrites, while slow cooling (un-chilled) produces large, coarse dendrites. Therefore, solidification over a temperature range is the primary requirement for dendrite growth. Primary austenite dendrites readily grow from the liquidus down to the eutectic temperature and growth of dendrites may also continue concurrently with the eutectic as the temperature decreases through eutectic range to the solidus. Thus, under cooling in case of chilled steel may lead to smaller dendrites and higher interaction. Hence, the eutectic cells solidify around these austenite dendrites and in this manner the entire microstructure is affected by the number and size of the dendrites.
Therefore the general picture of solidification of un-chilled steel (sand cast) and chilled steel composite with various eutectic cells, dendrite arm spacing, graphite shapes and matrix structures (as shown in figure 2, a to l) can be summarized as follows: The solidification of mild steel composite resulting from sand casting without a chill starts from a small number of nuclei as compared with chilled steels, a phenomenon indicated by eutectic cell count (see figure 2, e and h). Since the growth condition in the liquid are favourable, these nuclei start growing as soon as temperature below the equilibrium temperature in case of steel (un-chilled) and with maximum under cooling in the case of chilled steel.
Therefore the rate of solidification has a direct effect on the size and structure of the composite. Higher and steeper cooling rates (effect of chilling) result in smaller grain size since the reinforcing particles during solidification are trapped between growing dendrites ceasing the dendrite growth propagation.
Pearlite content.
From the microstructural observations (fig. 2, a to d), it can be seen that there exist a relationship between pearlite content and eutectic cell (fig. 2, i to l) for the various specimens cast using different type of chills. It is noteworthy that steel cast using copper chill contain cementite in fine pearlite matrix whereas un-chilled steel composite contain ferrite in coarse pearlite matrix. Table 3 sand 4 shows pearlite content present as well as the eutectic cell count for various chilled composite crushing jaws developed cast using copper chill blocks.
From the microstructural observations (fig. 2, a to d), it can be seen that there exist a relationship between pearlite content and eutectic cell (fig. 2, i to l) for the various specimens cast using different type of chills. It is noteworthy that steel cast using copper chill contain cementite in fine pearlite matrix whereas un-chilled steel composite contain ferrite in coarse pearlite matrix. Table 3 sand 4 shows pearlite content present as well as the eutectic cell count for various chilled composite crushing jaws developed cast using copper chill blocks.
Dendrite formation.
Results of the investigation indicate that the minimum eutectic temperature can be used as a measure of under-cooling that reflects DAS (fig 2, e to h), the number of cells (fig. 2, i and l) precipitated and the chilling tendency of the steel. Higher dendritic interaction areas in the case of chilled steel composites reflect the interweaving of dendrite through eutectic cells that effectively tie the eutectic cells together. Since dendrites are formed from primary austenite, they have a higher tensile strength than eutectic carbon. Here, due to chilling, dendrites grow directly from austenite and do not contain flake carbon. Instead they contain carbides (cementite) in the pearlite matrix as shown in fig. 2 (a to d). Table 5 shows dendrite arm spacing for various crushing jaw chilled composites cast using copper chill blocks.
Results of the investigation indicate that the minimum eutectic temperature can be used as a measure of under-cooling that reflects DAS (fig 2, e to h), the number of cells (fig. 2, i and l) precipitated and the chilling tendency of the steel. Higher dendritic interaction areas in the case of chilled steel composites reflect the interweaving of dendrite through eutectic cells that effectively tie the eutectic cells together. Since dendrites are formed from primary austenite, they have a higher tensile strength than eutectic carbon. Here, due to chilling, dendrites grow directly from austenite and do not contain flake carbon. Instead they contain carbides (cementite) in the pearlite matrix as shown in fig. 2 (a to d). Table 5 shows dendrite arm spacing for various crushing jaw chilled composites cast using copper chill blocks.
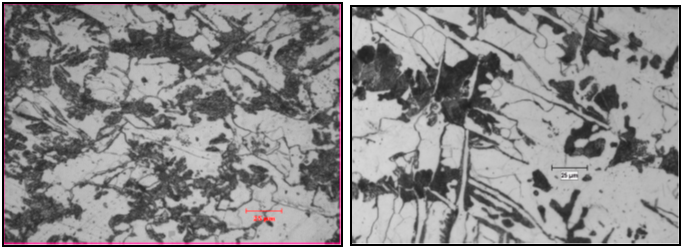
Figure 2: (a) Microstructure of 6 wt.% Figure. 2(b) Microstructure of 9 wt.% chilled steel composite (500 X) chilled steel composite (500 X).
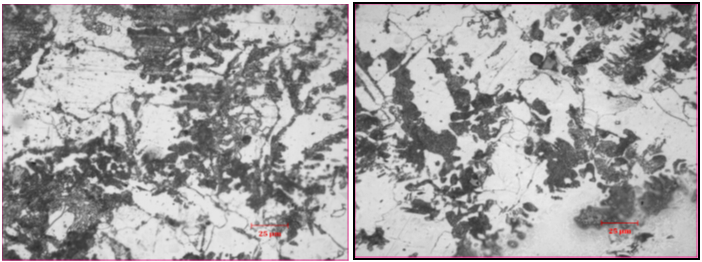
Figure 2: (c) Microstructure of 12 wt.% Figure. 2(d) Microstructure of 15wt.% chilled steel composite (500 X) chilled steel composite (500 X).
Figure 2: (a to d) Microstructure of different copper chilled steel composites.
Figure 2: (a to d) Microstructure of different copper chilled steel composites.
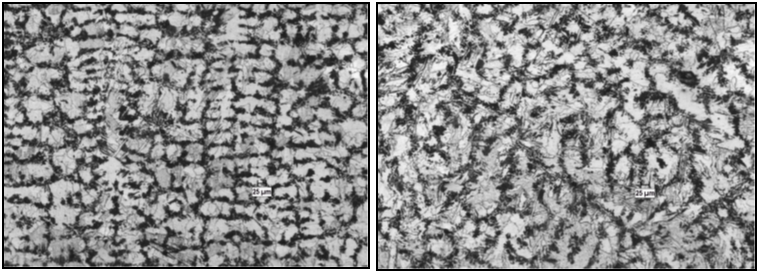
Figure 2: (e) Dendrite arm spacing of 6 wt.% Figure 2(f): Dendrite arm spacing of 9 wt.% chilled steel composite (500 X) chilled steel composite (500 X).
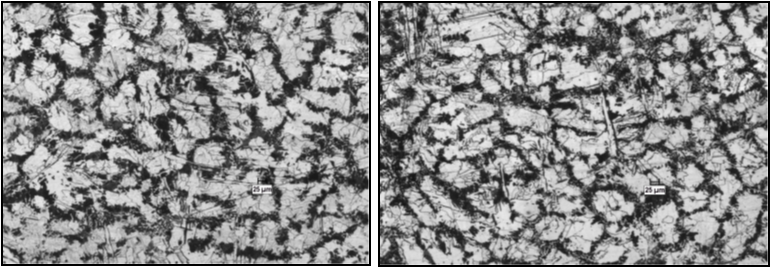
Figure 2: (g) Dendrite arm spacing of 12 wt.% Figure. 2(h): Dendrite arm spacing of 15 wt.% chilled steel composite (500 X) chilled steel composite (500 X).
Figure 2 (e to h): Dendrite arm spacing of different copper chilled steel composites
Figure 2 (e to h): Dendrite arm spacing of different copper chilled steel composites
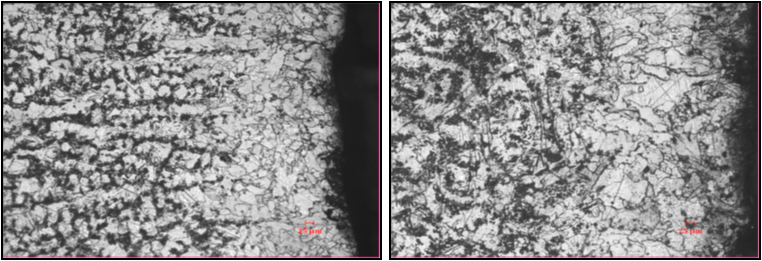
Figure 2: (i) Eutectic cell count of 6 wt.% Figure 2(j): Eutectic cell count of 9 wt.% chilled steel composite (50 X) chilled steel composite (50 X).
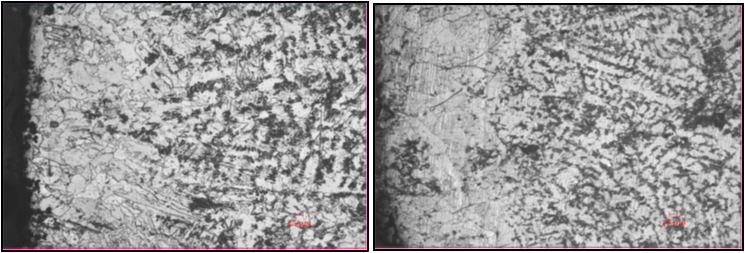
Figure 2: (k) Eutectic cell count of 12 wt.% Figure 2(l): Eutectic cell count of 15 wt.% chilled steel composite (50 X) chilled steel composite (50 X).
Figure 2 (i to l): Eutectic cell count of different copper chilled steel composites.
Figure 2 (i to l): Eutectic cell count of different copper chilled steel composites.
Pearlite content | ||||
3 wt.% | 6 wt.% | 9 wt.% | 12 wt.% | 15 wt% |
43 | 51 | 58 | 68 | 74 |
(Note: The remaining micro-constituents are cementite, ledeburite and ferrite)
Table 3: Pearlite content of various composites cast using copper chill.
Table 3: Pearlite content of various composites cast using copper chill.
Eutectic Cell Count (ECC) | ||||
3 wt.% | 6 wt.% | 9 wt.% | 12 wt.% | 15 wt% |
98 | 141 | 156 | 165 | 185 |
Table 4: Pearlite content of various composites cast using copper chill.
Dendrite Arm Spacing, DAS (mm) | ||||
3 wt.% | 6 wt.% | 9 wt.% | 12 wt.% | 15 wt% |
1 | 3 | 5 | 7 | 7 |
Table 5: Dendrite Arm Spacing (DAS) of various composites cast using copper chill.
Micro structural Observation of the Composite.
It is confirmed form the XRD spectrum peaks (Fig. not shown) that the of the composite developed indicates the presence of constituents of the matrix material as well as the reinforcement indicating that the reinforcement has thoroughly mixed in the matrix. Microstructure of the composite developed (fig 2 a to d) in the present research primarily depends on the rate of chilling as well as the reinforcement content that influences solidification. It is observed from the structural studies that the growth of Fe dendritic network structure is surrounded by W-Fe3C which is formed due to undercooling of the casting (chilling effect) during solidification. Also microstructural studies of chilled composite reveal fine grained structure without micro porosity. All the above microstructural integrity may due to density of the reinforcement particles associated with judicious location chill blocks as well as the stirring mechanism used to create vortex and wettability of the pre-heated reinforcement during stirring.
It is confirmed form the XRD spectrum peaks (Fig. not shown) that the of the composite developed indicates the presence of constituents of the matrix material as well as the reinforcement indicating that the reinforcement has thoroughly mixed in the matrix. Microstructure of the composite developed (fig 2 a to d) in the present research primarily depends on the rate of chilling as well as the reinforcement content that influences solidification. It is observed from the structural studies that the growth of Fe dendritic network structure is surrounded by W-Fe3C which is formed due to undercooling of the casting (chilling effect) during solidification. Also microstructural studies of chilled composite reveal fine grained structure without micro porosity. All the above microstructural integrity may due to density of the reinforcement particles associated with judicious location chill blocks as well as the stirring mechanism used to create vortex and wettability of the pre-heated reinforcement during stirring.
Effect of chilling during solidification has made proper flow of liquid metal into the inter-dendritic spaces making the bond strong without any porosity producing fine grained structure. However the grain refinement and reinforcement distribution is primarily attributed to the capacity of the reinforcement particulate to nucleate from the matrix alloy during solidification under the influence of chill that restricted the growth of grains. It can be seen from the microstructure that the particles are evenly distributed in the inter-dendritic regions for 3, 6, 9 and 12 wt.% reinforcement content with good bonding with the matrix and whereas for 15 wt.% reinforcement content, microstructure shows fewer particles at the inter-dendritic region. This may be due to the increase in density difference ensured at higher concentration of reinforcement within the matrix resulting in settling down and /or clustering of the reinforcement near the grain boundaries. But at higher percent addition of reinforcement ie., beyond 12 wt.% , it is observed that there is segregation/clustering of the reinforcement near the grain boundaries. Therefore adding reinforcement beyond 12 wt.% do not serve any purpose. Therefore all further focus of discussion is based on chilled MMCS containing 12 wt.% reinforcement.
Mechanical Behavior of the Chilled Composite (Strength and Hardness).
Recently, steel MMCs are being widely used as structural and automobile material owing to their increased strength coupled with an extremely good strength-to-weight ratio. This is primarily due to the fact that the composites transfer the applied load onto the harder reinforcements via the matrix metal. In order to realize this, an imperative chilling of composites was introduced in the present research to ensure a strong interfacial bonding between the different phases making up the composite dense, sound and free from micro-porosity. It is well known that the difference between co-efficient of thermal expansion of matrix and reinforcement leads to increase in dislocation density. This increase in dislocations will be inhibited near the grain boundaries, requiring higher energy (i.e. loading) to keep their movement across the grains. This is also one the reason for increase in UTS up to 12 wt. % addition of the reinforcement and addition of the particles beyond 12 wt. % decreases the strength and this decrease can be attributed to agglomeration and segregation of the particles towards the eutectic phase. The agglomerated particles would present a weaker zone in the structure, which may act as a crack initiator in the specimen and hence lowers the strength.
Recently, steel MMCs are being widely used as structural and automobile material owing to their increased strength coupled with an extremely good strength-to-weight ratio. This is primarily due to the fact that the composites transfer the applied load onto the harder reinforcements via the matrix metal. In order to realize this, an imperative chilling of composites was introduced in the present research to ensure a strong interfacial bonding between the different phases making up the composite dense, sound and free from micro-porosity. It is well known that the difference between co-efficient of thermal expansion of matrix and reinforcement leads to increase in dislocation density. This increase in dislocations will be inhibited near the grain boundaries, requiring higher energy (i.e. loading) to keep their movement across the grains. This is also one the reason for increase in UTS up to 12 wt. % addition of the reinforcement and addition of the particles beyond 12 wt. % decreases the strength and this decrease can be attributed to agglomeration and segregation of the particles towards the eutectic phase. The agglomerated particles would present a weaker zone in the structure, which may act as a crack initiator in the specimen and hence lowers the strength.
Strength and hardness tests were conducted only after subjecting the test samples to annealing heat treatment process to relieve all the stresses developed during casting. Table 6 shows the effect of reinforcement content on Ultimate Tensile Strength (UTS) for various chilled MMCs cast with different wt% reinforcement. It is observed from the microstructure as well from the strength test results that, increase in the reinforcement content increases UTS up to 12 wt.% and beyond which it decreases due to even distribution of the reinforcement and segregation near the grain boundary. These act as stress risers concentrated at that location fails to transfer the load and hence the strength falls.
In most cases, ceramic reinforced MMCs have superior mechanical properties compared to the un-reinforced matrix alloy because these MMCs have high dislocation densities due to dislocation generation as a result of differences in coefficient of thermal expansion [12]. As in this study however, with the incorporation of WC particulate reinforcement has a major effect in improving mechanical properties. Strength test results reveal that the UTS of the matrix alloy (ASTM A216 steel) used in the present research is around 258 N/mm2. Whereas in the present research, the UTS obtained for chilled steel reinforced with WC particulate cast using copper chill blocks, UTS ranges from 282 to 488 N/mm2 (strength increased by about 35%). Hence it is observed that the strength of chilled steel composite was found to increase by 35 % as compared against the matrix alloy. The increase in UTS suggests that WC particulate as reinforcement and chilling has an effect on the UTS. This is in consistence with the past research which indicates that the strength of the composite depends on the reinforcement, interfacial bond between the matrix and the reinforcement, distribution of the particles as well as on the size of the particles [13]. But in the present investigation in addition to all the above parameters, sound casting with fine grain structure was obtained due to chilling, vortex method of stirring and preheating of the reinforcement has played a vital role in further increasing the UTS. Microstructural studies also reveal that chilled steel MMCs are denser without any micro-porosity is also the reason for the increase in UTS. From the results of the mechanical characterization of chilled steel reinforced with WC, one can conclude that strength depends on reinforcement content and chilling effect.
UTS (MPa) | ||||
3 wt.% | 6 wt.% | 9 wt.% | 12 wt.% | 15 wt% |
282.55 | 347.33 | 456.56 | 488.67 | 436.35 |
Table 6: UTS of various chilled composites cast using copper chill (average value of UTS of plane carbon steel is 258 Mpa).
In order to confirm the above discussions, fractographic analysis of the specimens failed in strength test was undertaken using SEM. Fig.3 (a to e) shows the SEM fractographs (at 100 X and 100 µm) of the fractured specimens containing 6, 9,12 and 15 wt. % reinforcement chilled MMC as well as the un-chilled matrix alloy. It is observed that for the matrix alloy, fracture was in ductile mode containing dimples (Fig. 3e) and failure is due to propagation of the cracks near the grain boundary. Here again the size of the dimples present in the fractured surface depends on the silicon content of the alloy. For chilled steel MMC with 12 wt% reinforcement content, the composite has become little brittle and the SEM of the fractured sample (Fig. 3d) showed mixed mode of fracture.
At higher percent of addition of reinforcement beyond 12 wt%, cluster formation of the reinforcement was observed in the microstructure with poor interfacial bonding that has caused the trans- granular type of brittle fracture (one of the reasons for decrease in mechanical properties). Therefore the size of the dimples in the fracture surface exhibits a direct proportional relationship with strength and ductility of the chilled composite i.e., finer the dimple size increases the strength and ductility of the chilled steel MMCs developed. It is well known and documented by several researchers [10,11] that ductility of discontinuous reinforced MMC’s decreases with an increase in reinforcement content. Hence the percent elongation is always inversely proportional to UTS. This is one of the reason that reinforcement has an effect only up to certain amount of reinforcement addition.
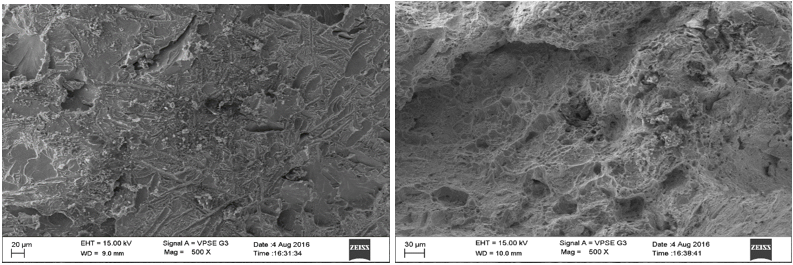
Figure 3: (a): Fractograph of 6 wt.% Figure 3(b): Fractograph of 12 wt.% chilled steel composite (20 µm) chilled steel composite (20 µm).
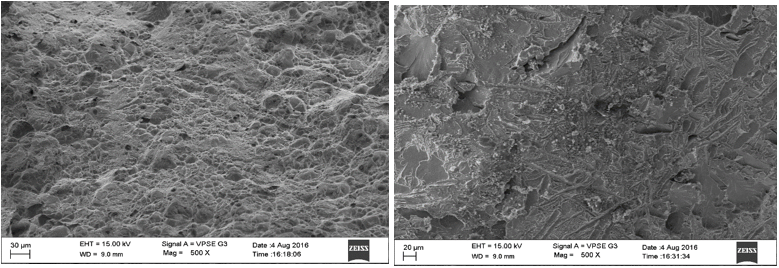
Figure 3: (c): Fractograph of 12 wt.% Figure 3(d): Fractograph of 52 wt.% chilled steel composite (20 µm) chilled steel composite (20 µm).
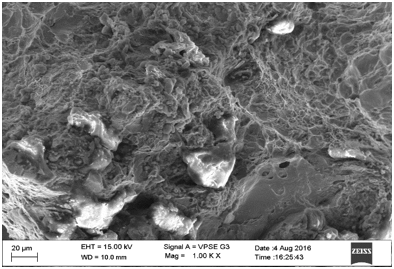
Figure 3e: Fractograph of un-chilled matrix steel (20 µm).
Figure 3: Fractographs of different specimens failed in tension test.
Figure 3: Fractographs of different specimens failed in tension test.
Table 7 shows hardness of chilled steel composite containing different wt. % reinforcement cast using copper chill blocks. The results of Rockwell hardness test (HRC) conducted on chilled composite samples revealed an increasing trend in matrix hardness with an increase in reinforcement content (up to 12 wt. %). Results of hardness measurements thus revealed that reinforcement content has an effect on hardness of the composite. This significant increase in the hardness can be attributed primarily to presence of harder ceramic (WC) particulates in the matrix that has higher constraint to the localized deformation during indentation because of reduced grain size due to chilling. In ceramic-reinforced composites, there is generally a big difference between the mechanical properties of the reinforcement and those of the matrix. These results in incoherence and a high density of dislocations near the interface between the reinforcement and the matrix [14]. Precipitation reactions are accelerated because of incoherence and the high density of dislocations act as heterogeneous nucleation sites for precipitation [15].
Hardness (Rockwell-C) | ||||
3 wt.% | 6 wt.% | 9 wt.% | 12 wt.% | 15 wt. % |
91 | 101 | 121 | 132 | 135 |
Table 7: Hardness (Rockwell-C) of various chilled composites cast using copper chill (average value of hardness of plane carbon steel is 79 HRC).
It is observed from the results of the hardness test that hardness of the composite increases linearly (up to 12 wt. % addition) as the reinforcement increases and maximum harness observed was 132 HRC. This increase in hardness in turn increases the wear resistance of the composite developed that suits jaw of the crusher, roller and automotive application. It is observed form the Table 7 that beyond 12 wt. % addition, the hardness decreases because of cluster formation and segregation of the reinforcement as evident from the microstructural studies. Copper end chill blocks used in the present research too has an effect on the hardness of the composites developed since chilling refines the grains in reducing the grain size that again offers resistance to indentation. It is also observed that maximum hardness was observed for all the composites developed was near the chill surface.
From the cast metal data hand book [15] it was found that hardness of the matrix material (ASTM A216 steel) used in the present research is around 79 HRC. Whereas in the present research, the hardness obtained for chilled steel reinforced with WC reinforcement cast using steel chill ranges from 91 HRC to 132 HRC (hardness increases by about 23%). It is observed that that hardness of chilled steel composite was found to be increased by 19 % as compared against the matrix alloy. The increase in hardness suggests that WC particulate as reinforcement and chilling has strong effect on the hardness.
Therefore, it is also observed from the results of strength and hardness test that chilled steel composite is found to be superior compared to matrix steel. Improvement in strength and hardness in the case of copper chilling is because of high volumetric heat capacity (VHC) which has resulted in carbide formation in the fine pearlitic matrix (see fig.2, a) during solidification, reinforcement content present as well as the composition of the steel. It is finally observed that addition of reinforcement to base steel and chilling increases the ultimate strength by about 35 % and hardness by 23 % near the chill end as compared with the matrix steel.
Tribological Behavior of the Composite.
Friction and wear
Table 8 (a to c) and table 9 shows the percent weight loss and coefficient of friction of steel composite containing 3, 6, 9, 12 and 15wt.% reinforcement as a function of sliding distance tested at a loads 20, 40 and 60 N respectively. At the lowest load (20 N) in mild wear regime with a high coefficient of friction and weight loss was always found for the chilled steels tested containing 3 wt.% reinforcement. As the load and sliding distance increases proportionately the weight loss increases. It can be seen form table 8 that as the reinforcement content and sliding distance increases, the weight loss decreases (or wear resistance increases). At higher loads (60 N), the chilled steel containing 3 wt.% reinforcement experienced high coefficient of friction and the same reduces as the reinforcement content and sliding distance increases. This shows that there is inverse relationship between weight loss and coefficient of friction for the same variation of sliding distance and reinforcement content. It is also observed that the chilled steel composite (3 wt.% reinforcement), tested at all loads underwent large weight loss during the early stages of the test. After sliding for some distance, the weight loss increased approximately linear with sliding distance. The sliding distance for transition from severe to mild wear could be identified by two factors: Firstly, by abrupt and steep reduction in the frictional force, and secondly, by change in the magnitude of displacement of pin specimen [16].
Friction and wear
Table 8 (a to c) and table 9 shows the percent weight loss and coefficient of friction of steel composite containing 3, 6, 9, 12 and 15wt.% reinforcement as a function of sliding distance tested at a loads 20, 40 and 60 N respectively. At the lowest load (20 N) in mild wear regime with a high coefficient of friction and weight loss was always found for the chilled steels tested containing 3 wt.% reinforcement. As the load and sliding distance increases proportionately the weight loss increases. It can be seen form table 8 that as the reinforcement content and sliding distance increases, the weight loss decreases (or wear resistance increases). At higher loads (60 N), the chilled steel containing 3 wt.% reinforcement experienced high coefficient of friction and the same reduces as the reinforcement content and sliding distance increases. This shows that there is inverse relationship between weight loss and coefficient of friction for the same variation of sliding distance and reinforcement content. It is also observed that the chilled steel composite (3 wt.% reinforcement), tested at all loads underwent large weight loss during the early stages of the test. After sliding for some distance, the weight loss increased approximately linear with sliding distance. The sliding distance for transition from severe to mild wear could be identified by two factors: Firstly, by abrupt and steep reduction in the frictional force, and secondly, by change in the magnitude of displacement of pin specimen [16].
Based on these measurements, the wear analysis are characterized by two distinct forms: which correspond to severe and mild wear conditions. Chilled steel composite 3e4showed steady state mild wear from the beginning of the test. At no point during the tests, severe wear was noticed for the composite containing higher ranges of the reinforcement content. It was also observed that, the sliding distance and weight loss during the severe wear regime decreases with an increase the reinforcement content. In the severe wear regime, wear rate of all the chilled steel composite decrease with increasing the reinforcement content. Hence the transition to lower wear rates (mild wear regime) is accelerated with increasing the reinforcement content in steel. It is obvious that chilling and reinforcement content effectively prevents the time/distance required for transition from severe to mild wear.
Sliding distance M | Weight loss (%) of different composites | ||||
3 wt.% | 6 wt.% | 9 wt.% | 12 wt.% | 15 wt.% | |
500 | 6.1 | 4.2 | 2.0 | 1.5 | 0.8 |
1000 | 6.3 | 4.8 | 2.6 | 1.8 | 1.0 |
1500 | 7.2 | 5.0 | 3.2 | 2.1 | 1.1 |
2000 | 9.3 | 5.4 | 4.1 | 2.2 | 1.4 |
2500 | 12.1 | 5.9 | 5.5 | 2.4 | 1.6 |
3000 | 14.5 | 6.4 | 5.8 | 2.8 | 1.9 |
Table 8 (a): Weight loss (%) of different composites tested at different sliding distances at 20 N load.
Sliding distance M | Weight loss (%) of different composites | ||||
3 wt.% | 6 wt.% | 9 wt.% | 12 wt.% | 15 wt.% | |
500 | 7.3 | 5.0 | 4.3 | 3.5 | 1.3 |
1000 | 8.4 | 6.1 | 4.9 | 3.6 | 1.5 |
1500 | 10.7 | 6.7 | 5.0 | 4.3 | 1.7 |
2000 | 13.7 | 7.5 | 5.0 | 4.5 | 1.7 |
2500 | 16.8 | 7.9 | 6.7 | 4.9 | 1.9 |
3000 | 18.4 | 8.1 | 7.4 | 5.2 | 2.1 |
Table 8 (b): Weight loss (%) of different composites tested at different sliding distances at 40 N load.
Sliding distance M |
Weight loss (%) of different composites | ||||
3 wt.% | 6 wt.% | 9 wt.% | 12 wt.% | 15 wt.% | |
500 | 8.4 | 6.8 | 5.4 | 2.8 | 1.8 |
1000 | 8.9 | 7.3 | 5.6 | 2.8 | 2.1 |
1500 | 10.8 | 7.8 | 6.1 | 3.6 | 2.2 |
2000 | 14.8 | 7.9 | 6.6 | 4.8 | 2.7 |
2500 | 18.3 | 8.7 | 7.9 | 6.0 | 2.9 |
3000 | 20.3 | 10.3 | 8.7 | 7.4 | 3.2 |
Table 8 (c): Weight loss (%) of different composites tested at different sliding distances at 60 N load.
The mean steady state values of the coefficient of friction (?) as a function of sliding speed tested at 60 N load is depicted in table 9 for both the chilled steel composite containing 3, 6, 9, 12 and 15 wt.% reinforcement respectively. At the lowest applied load of 20 N and at the lowest sliding speed of 500 m, a coefficient of friction about 0.73 was observed for steel composite containing 3 wt.% reinforcement in the mild wear regime and it was reduced to 0.68 as shown n the table. At intermediate sliding speed (2000 m) the coefficient of friction decreases in the mild wear regime and finally at higher sliding speeds (3000 m) all the steels displayed very low coefficient of friction around 0.2. At the highest applied load of 60 N (as shown in table 9) and at the lowest sliding speed a high coefficient of friction of 0.97 was measured for chilled steel containing 3 wt.% dispersoid content severe wear regime , whereas the chilled steels tested at the same load (60 N) at different sliding distance, the coefficient of friction was decreased as the reinforcement content increases. Therefore the coefficient of friction tested at the highest load (60 N) for 3 wt.% reinforcement chilled steel for different sliding distance lies between 0.97 and 0.83.
Sliding distance M |
Coefficient of friction (µ) | ||||
3 wt.% | 6 wt.% | 9 wt.% | 12 wt.% | 15 wt.% | |
500 | 0.97 | 0.89 | 0.64 | 0.67 | 0.72 |
1000 | 0.97 | 0.83 | 0.61 | 0.61 | 0.60 |
1500 | 0.89 | 0.84 | 0.61 | 0.53 | 0.49 |
2000 | 0.85 | 0.87 | 0.58 | 0.47 | 0.31 |
2500 | 0.83 | 0.89 | 0.51 | 0.32 | 0.21 |
3000 | 0.83 | 0.73 | 0.40 | 0.21 | 0.18 |
Table 9: Coefficient of friction (as indicated by the wear testing machine) of different composites tested at different sliding distances at 60 N load.
Effect of Reinforcement Content on Severe Wear
Effect of chilling and reinforcement content changes the microstructure of the un-chilled steel composite (ferrite in coarse pearlitic matrix) and thus affects the wear behavior. The observation made using the optical microscope (fig. 2 a to d) clearly reveals cementite contained in pearlite matrix is accompanied by the deformation and hence the micro cracks. The depths of the deformation zone where the cementite was deformed, was measured in order to obtain the depth of the plough region. Microstructural studies indicates that these depths were found to be 34 mm for chilled steel containing 3 wt.% reinforcement and 12 mm for steel containing 15 wt.% reinforcement. It was also observed that the depth of the deformation zone decreases with increasing the reinforcement content in steel. Further, the cracks propagate in the subsurface as a result of adhesion and deformation. In the beginning of the wear test, the plastic flow of the ferrite for steel cast using 3 wt.% reinforcement was appreciable and thus causes severe wear.
Effect of chilling and reinforcement content changes the microstructure of the un-chilled steel composite (ferrite in coarse pearlitic matrix) and thus affects the wear behavior. The observation made using the optical microscope (fig. 2 a to d) clearly reveals cementite contained in pearlite matrix is accompanied by the deformation and hence the micro cracks. The depths of the deformation zone where the cementite was deformed, was measured in order to obtain the depth of the plough region. Microstructural studies indicates that these depths were found to be 34 mm for chilled steel containing 3 wt.% reinforcement and 12 mm for steel containing 15 wt.% reinforcement. It was also observed that the depth of the deformation zone decreases with increasing the reinforcement content in steel. Further, the cracks propagate in the subsurface as a result of adhesion and deformation. In the beginning of the wear test, the plastic flow of the ferrite for steel cast using 3 wt.% reinforcement was appreciable and thus causes severe wear.
But in the case of steel containing 6 and 9 wt% reinforcement, the formation of a hard surface consisting of carbides in pearlitic matrix helps in preventing adhesion. As a result, transition from severe wear to mild wear occurs and concomitantly the wear rate is reduced as a result of removal of wear debris as a lower rate. In steel composites containing 12 and 15 wt.% reinforcement, the deformation are prevented because of the beneficial effects of the reduced grain size (chilling effect) and the hard reinforcement content in higher ranges. Therefore it is considered that severe wear caused by the adhesion disappears with increasing the reinforcement content.
Effect of Reinforcement Content on Mild Wear.
It is observed that for the chilled steel cast composite containing 3 wt.% reinforcement, worn surface was completely smooth and flat and contained wear tracks in the direction of sliding. In addition, the signature of plastic flow is not at all observed in the subsurface. In contrast, the worn surface of chilled steel composite was found to be rough. Microscopic examination of its subsurface shows fragmentation and their uniform dispersion on the entire worn surface and, as a result, plastic flow is very limited. Further, in the case of chilled steel composite containing 12 and 15 wt. % reinforcement, the surface found to be very rough with a characteristic brittle fracture. The subsurface region consisted of fragments of crushed (viewed under the microscope).
It is observed that for the chilled steel cast composite containing 3 wt.% reinforcement, worn surface was completely smooth and flat and contained wear tracks in the direction of sliding. In addition, the signature of plastic flow is not at all observed in the subsurface. In contrast, the worn surface of chilled steel composite was found to be rough. Microscopic examination of its subsurface shows fragmentation and their uniform dispersion on the entire worn surface and, as a result, plastic flow is very limited. Further, in the case of chilled steel composite containing 12 and 15 wt. % reinforcement, the surface found to be very rough with a characteristic brittle fracture. The subsurface region consisted of fragments of crushed (viewed under the microscope).
This shows that mild wear in steels composites are dominated by their reinforcement content. A very thin wear induced layer was formed on the entire surface and, in addition some carbide was also projected onto the surface. The lengths of the crushed carbides were measured for more than 10 fragments on the several cross sectional micrographs. The mean length was found to be 6 mm (ranging from 4.5 to 8 mm) for steel containing 15 wt.% of reinforcement. From these detailed observations, it becomes obvious that the carbides present were crushed into small fragments and a thin layer is formed on the smooth surface containing wear tracks confirming abrasive wear in the mild wear regime.
Analysis of Wear Mechanism by SEM
Figure 4 (a to e) shows SEM photograph of the worn surfaces of chilled steel composites (cast with different reinforcement content) and un-chilled steel tested in the mild wear regime. Wear mechanism of the present investigation is suggested by two modes. Mode-1 refers to adhesive wear (severe wear) and is predominant in the un-chilled steel composite and also in steel composite containing 3 wt.% reinforcement tested at higher loads. This type of wear disappears as the reinforcement content increases. On the other hand, Mode-2, which is essentially abrasive wear (mild wear) as result of embedded hard carbide particles in steels exposed on the worn surface and the loose fragments between two surfaces, dominates in steels containing higher reinforcement content ie., beyond 9 wt.%.
Figure 4 (a to e) shows SEM photograph of the worn surfaces of chilled steel composites (cast with different reinforcement content) and un-chilled steel tested in the mild wear regime. Wear mechanism of the present investigation is suggested by two modes. Mode-1 refers to adhesive wear (severe wear) and is predominant in the un-chilled steel composite and also in steel composite containing 3 wt.% reinforcement tested at higher loads. This type of wear disappears as the reinforcement content increases. On the other hand, Mode-2, which is essentially abrasive wear (mild wear) as result of embedded hard carbide particles in steels exposed on the worn surface and the loose fragments between two surfaces, dominates in steels containing higher reinforcement content ie., beyond 9 wt.%.
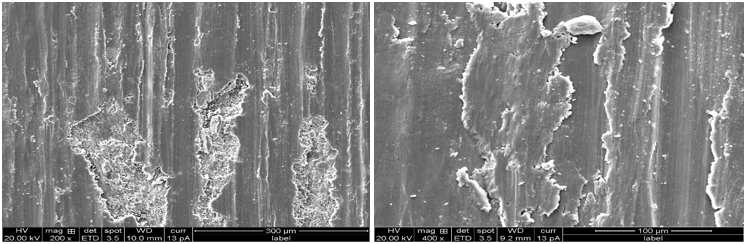
Figure 4: (a): Worn surface of 6 wt.% Figure 4(b): Worn surface of 9 wt.% chilled steel composite (50 µm) chilled steel composite (50 µm).
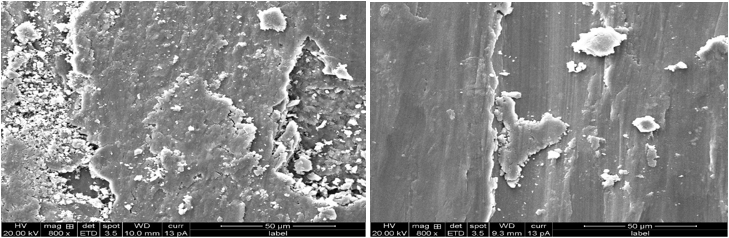
Figure 4: (c): Worn surface of 12 wt.% Figure 4(d): Worn surface of 15 wt.% chilled steel composite (50 µm) chilled steel composite (50 µm)
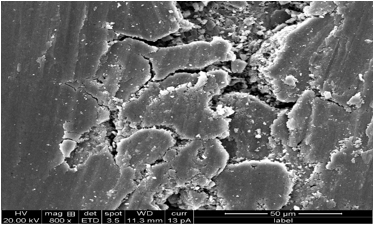
Figure 4e: Worn surface of un-chilled matrix steel (50 µm).
Figure 4 (a to e): SEM photographs of worn surface of different chilled steel composites.
Figure 4 (a to e): SEM photographs of worn surface of different chilled steel composites.
SEM of the worn surface examination reveals that the surface of the chilled steel composite consists of both hardened and deformation layers. The structure of the hardened layer consists mainly of the fragmented carbide phase. The depth of this layer depends on the applied load and is in the vicinity of 8 to 22 mm. However, the depth of the hardened layer in the steel is markedly reduced by increasing the chilling rate. Moreover, the hardness value of the hardened layer in the chilled steel is considerably higher than that of the un chilled steel composite. Because of limited plastic deformation in the mild wear regime, composites containing high reinforcement content (9 and 15 wt.%), micro structural studies reveal that, the fragmentation of the carbide appears as brittle fracture and in the case of un-chilled steel the plastic flow is due to deformation of ferrite.
Relationship between Load, Microstructure and Wear.
In the two body abrasion, the major portion of the load applied during testing is transferred to the specimen and the wear of the material took place under high stress condition [17]. This is supported by the experimental results, as evident by the increase in transition load from severe to mild wear is dependent on the reinforcement content as well as with the chilling [18]. These explanations are in line with earlier reports of Moustafa [19] that have shown an increase in the load for transition from mild to severe wear.
In the two body abrasion, the major portion of the load applied during testing is transferred to the specimen and the wear of the material took place under high stress condition [17]. This is supported by the experimental results, as evident by the increase in transition load from severe to mild wear is dependent on the reinforcement content as well as with the chilling [18]. These explanations are in line with earlier reports of Moustafa [19] that have shown an increase in the load for transition from mild to severe wear.
On the similar grounds, in the present research, hard tungsten carbide particles (reinforcement) in chilled steel composite act as protuberances in the peralitic matrix and bear the major portion of load and as a consequence, protect steel from wear. This leads to the reduction in weight loass of chilled steel due to reinforcement of particles in the pearlitic matrix. Note that the weight loss is significantly dependent on the applied load, microstructure. Hardness, chilling rate and reinforcement content of the material. It is observed that the cutting efficiency of the disc particles increases with an increase in the applied load. As a result, more material is removed at higher loads and hence the wear rate increases with an applied load. The depth and width of cutting grooves also depends on the hardness of the material [20]. Since the hardness of the un-chilled steel is lower than that of the chilled steels and hence, the wear rate of chilled steel composites becomes lower than that of the un-chilled steel. Therefore, the chances of fracturing of carbide particles in the pearlitic matrix are less in the case of chilled steel composites. This led to considerably higher wear resistance of the chilled steel composites even at a high load regime. As a result, the removal of a material vis-à-vis the wear rate of the material is governed by deformation parameters, microstructure and hardness. Thus by increasing the strength and hardness due to of pearlitic matrix in the chilled steel composites, the cutting efficiency of the hard disc particles is reduced.
Relationship between Hardness and Wear
It is well known that the wear resistance of the material increases with hardness irrespective of the applied load. SEM studies of the chilled steel composites tested at different loads reveal that, at lower load (20 N), the variation of wear rate with hardness was marginal, but at higher load (60 N) considerable wear with hardness was noted. At lower load, mainly cutting type wear takes place and the subsurface deformation is negligible [21]. The reinforcement particles remain intact within the pearlitic matrix and protect the specimen surface more effectively. Thus, at lower load, the surface deformation behavior is negligible. At the higher load, both cutting and ploughing types of mechanisms are operating and the subsurface deformation becomes considerably high. Because of subsurface deformation, transverse and longitudinal cracks are generated on the wear surface [22].
It is well known that the wear resistance of the material increases with hardness irrespective of the applied load. SEM studies of the chilled steel composites tested at different loads reveal that, at lower load (20 N), the variation of wear rate with hardness was marginal, but at higher load (60 N) considerable wear with hardness was noted. At lower load, mainly cutting type wear takes place and the subsurface deformation is negligible [21]. The reinforcement particles remain intact within the pearlitic matrix and protect the specimen surface more effectively. Thus, at lower load, the surface deformation behavior is negligible. At the higher load, both cutting and ploughing types of mechanisms are operating and the subsurface deformation becomes considerably high. Because of subsurface deformation, transverse and longitudinal cracks are generated on the wear surface [22].
Subsequently, because of cold working, the subsurface is also work hardened [23]. The subsurface deformation is governed by the mechanical properties such as hardness, ductility and strength, which are again influenced by the microstructure and distribution of hard carbide particles. These may cause considerable reduction in the wear rate with an increase in hardness and strength when tests are conducted at higher applied load. The sub surface deformation of the chilled steel composites may vary because of different matrix micro-structure and mechanical properties. In addition to the initial hardness of the chilled steel composites, after a few cycles of motion of the sample against the abrasive media, the hardness of the wear surface of different samples increases. Apart from this, since the reinforcement particles are very fine (as viewed under the microscope) and they may have the tendency to break into small particles and spread over the wear surface thus protecting the pearlitic matrix from severe wear.
It is also observed through the microscope that the fragmented reinforcement particles were present in the subsurface region for chilled steel composites containing high reinforcement content in severe wear regime. This includes higher hardness of the surface of the chilled samples than their bulk hardness during testing. This in turn results in a significantly lower wear rate in the chilled steel composites as compared with the un-chilled steel tested at higher applied loads. The cracking and removal of flaky materials and work hardening of the subsurface take place simultaneously over the specimen surface. The overall wear rate of the material would depend on the cutting action and work hardening rate of the chilled steels may be higher and it increases with an increase in hardness. Apart from this, the possibility of fracture and fragmentation of reinforcement particles may be low in chilled steel composites because of the strong and hard carbides in the pearlitic matrix due to the effect of chilling. In fact the wear characteristics of the chilled steel composites are governed by the interaction of their chilling effect, reinforcement content and its hardness.
g) Worn Surface Analysis and Wear Debris.
Wear debris generated during the mild wear regime was collected after the end of the wear test and examined under the microscope. The shape of the wear debris was mostly large and irregular in the case of the un-chilled steel and in case of chilled steel composites it was few and fine. From the observations of the worn surfaces and sub surfaces of chilled steel composites, it is clear that the generation and removal of wear debris is affected by the fragmentation of reinforcement particles. From SEM studies (Figure 4) it is recognized that reinforcement particles in wear debris were small and irregular in shape with sharp edges. It is observed from the results that the size of the wear debris decreases whereas the reinforcement fragments remain more or less the same with increase in volume fraction of carbides. The reason for decrease in the size of the debris is as follows. Under compression, a brittle body is made smaller by crack propagation until a critical size and also due to non-attachment of it to the pearlitic matrix of the material. But the reinforcement below this size are deforming slightly rather than rapid cracking.
Wear debris generated during the mild wear regime was collected after the end of the wear test and examined under the microscope. The shape of the wear debris was mostly large and irregular in the case of the un-chilled steel and in case of chilled steel composites it was few and fine. From the observations of the worn surfaces and sub surfaces of chilled steel composites, it is clear that the generation and removal of wear debris is affected by the fragmentation of reinforcement particles. From SEM studies (Figure 4) it is recognized that reinforcement particles in wear debris were small and irregular in shape with sharp edges. It is observed from the results that the size of the wear debris decreases whereas the reinforcement fragments remain more or less the same with increase in volume fraction of carbides. The reason for decrease in the size of the debris is as follows. Under compression, a brittle body is made smaller by crack propagation until a critical size and also due to non-attachment of it to the pearlitic matrix of the material. But the reinforcement below this size are deforming slightly rather than rapid cracking.
Under the mild wear conditions, it is observed in particular at the lowest load (20 N), the worn surfaces of the tested chilled steel composites were characterized by the presence of an oxide compact layer (about 8 mm) comprised of iron oxide. The presence of iron oxide is due to the abrasive action of the pin on the steel counter face. Wear debris collected under conditions were in the form of very fine and rounded particles. Experimental analyses showed that they were mainly comprised of Fe2O3 and Fe3C. On the contrary, the micro structural observation reveal rough worn surfaces with grooves along the sliding direction were observed in the severe wear regime. They were metallic in appearance, with some dark zones comprised of a mechanical mixed layer [24] containing metallic iron, iron oxides and carbide fragments as confirmed by experimental analyses. According to Zhang et al [25] in the mild wear regime, always observed at the lowest applied load (20 N), the worn surfaces of both the un-chilled steel and the chilled steels were characterized by the presence of a protective iron-oxide rich transfer layer, suggesting that a material transfer process was active. Wear proceeded by spalling of this layer, producing fine and rounded oxide debris. The presence of carbide particles in chilled steels act as a load bearing phase, limiting plastic flow and wear of the matrix. But at the same time plough into the steel abrasive wheel produces debris. These are continuously oxidized during sliding and transferred onto the counter facing sliding surfaces.
Longitudinal cross sections of the wear scars also analyzed by optical microscope and SEM to characterize the subsurface deformation and to explain the superior wear resistance of the chilled steel with respect to the un-chilled steel composite. Micro-hardness tests on the longitudinal cross-sections of the same samples as a function of depth beneath the worn surfaces were carried out in order to evaluate the depth of the affected zone. In the case of chilled steel with maximum reinforcement content (15 wt.%), two layers were found under the very hard and brittle layer: a first soft layer (about 150 mm) whose hardness was about 128 HRC and a second hardened layer (about 50 mm) with a hardness about 118 HRC. These results are in agreement with those obtained by Venkataraman et al [26], who also observed a soft layer wherein the flow stress decreases with increasing shear strain, followed by a hardening layer, wherein the flow stress increases with increasing strain. The authors related the presence of the soft layer to the formation of ferrite at the coarse pearlite matrix and such ferrite prevent efficient transfer of load from the pearlitic matrix and thus lower the strength of the chilled steels. Conversely, a slight strain-hardening in the shear zone (depth about 250 mm) just beneath the soft layer, was found that the plastic deformation occurred at a higher depth, while the presence of the soft layer was not found.
Chilled Steel Composite Crusher Jaw and its Operation
Jaw type of crushers are being popularly used for crushing stone to pebbles. Presently the jaw of the crusher is made of steel substrate on which hard facing is provided by tungsten carbide particles in the form of welding. After using the crushing machine for one day (average 6 hours of operation per day), the jaw is to be replaced for hard facing. Results of the present chilled steel composite jaw (containing 12 wt.% reinforcement) show that, even after using the jaw for one week, the jaw face contain few indentations of 2 mm depth spread over the entire jaw, but this jaw can be further used successfully.
Jaw type of crushers are being popularly used for crushing stone to pebbles. Presently the jaw of the crusher is made of steel substrate on which hard facing is provided by tungsten carbide particles in the form of welding. After using the crushing machine for one day (average 6 hours of operation per day), the jaw is to be replaced for hard facing. Results of the present chilled steel composite jaw (containing 12 wt.% reinforcement) show that, even after using the jaw for one week, the jaw face contain few indentations of 2 mm depth spread over the entire jaw, but this jaw can be further used successfully.
Conclusions
In this research, characterization of wear behavior of chilled steel composites containing different wt.% reinforcement cast using copper chill during solidification was studied. The results can be summarized as follows.
- Microstructure, eutectic cell count and dendrite arm spacing of the chilled steel composites are finer than that of the un-chilled steel with random orientation of reinforcement particles in pearlite matrix.
- Strength, hardness and wear resistance of the chilled steel composites are superior to those of the un-chilled steel. It was found that these properties increase with an increase in reinforcement content in fine pearlite matrix.
- At the lower load, chilled steel composites exhibited mild wear regime with high coefficient of friction and at higher loads they exhibited severe wear with better wear resistance than the un-chilled steel composite.
- Size of the wear debris decreases because of rapid crack propagation of a brittle body under compression whereas the size of the reinforcement fragmentation remain approximately the same.
References
- Joel Hemanth. (2003). “Effect of high rate of heat transfer during solidification of alloyed cast iron using water-cooled and sub-zero chills on mechanical behavior”, Materials and Design, Elsevier Sc., 24, 37-45.
- J. Y. Huang, X.Z. Liao, et. al., (2003). “Microstructure of cryogenic treated M2 tool Steel”, Materials Science and Engineering- A, 339, 241-244.
- D.N. Collins, J. Dormer. (1997). “Deep cryogenic treatment of a D2 cold work tool Steel”, Heat Treatment of Metals, 3, 71-79.
- R.F. Barron. (1973). “Effect of cryogenic treatment on lathe tool wear”, Refrigeration Sc. and Technology, 33. 529-537.
- F. Meng, K. Tagashira. (1994). “Wear resistance and microstructure of cryogenic treated Fe-1.4Cr-1C bearing steel”, Scri. Metall. Mater. 31, 865-873.
- Bensely, A. Prabhakaran, D.Mohan Lal and G.Nagarajan. (2006). “Enhancing the wear resistance of case carburized steel (En353) by cryogenic treatment”, Cryogenics. 45, 747-754.
- M. Raza Batne, J.A.Szpuran, X.Wang and D.Y.Li. (2006). Wear and Corrosion wear of medium carbon steel, Wear, 260, 116-122.
- Chen Zhenhua, Tang Jie, Chen Gang and Yan Hongge. (2007). “Effect of Si content and thermo-mechanical treatment on dry sliding wear behavior”, Wear, 262, 362- 368
- A.S. Shafaat Ahmed, M.A. Haseeb and A.S.W. Kurny. (2007). “Study of wear behavior of Al-4.5% Cu-3.4% Fe in situ composite”, J. of Materials Processing Technology, 182, 327-332
- Joel Hemanth. (1996). Wear characteristics of sub zero chilled cast iron, Wear, Elsevier Sc.,192, 134-143.
- Joel Hemanth, (1998). Effect of cooling rate on the dendrite arm spacing and Ultimate tensile strength of cast iron, Material Science, Elsevier Sc., 33, 23-35.
- B.K. Prasad and O.P Modi and A.K. Jha, (1994). Metallurgical aspects of Al based composites, Tribology Int. 27, 153-158.
- Textron Specialty Materials, (1992). “Continuous Silicon Carbide Metal Matrix Composites”, Lowell, MA: Textron, 45-57.
- D.P. Mondal, S. Das, Y.L. Saraswati, O.P. Modi, (2000). “Stir casting of aluminum based composites”, Aluminium. Trans, 2, 215-222.
- P.K. Rohatagi, R. Asthana and S. Das, (1986). “Solidification of Aluminum based composites, Inst. of Metals, 31, 115-124.
- M. Tsutsui, Y. Yamada, (1996). “Wear of Al-ZrO2-Fe3C hybrid composite materials” Japan. Inst. of Metals. 56: p. 271.
- Y. Iwai and H. Honda, (1995). “Sliding wear behavior of SiC whisker reinforced Al Composites”, Wear 181, 594-602.
- B.K. Prasad, S. Das and A.K. Jha, (1997). “Dry sliding wear of Al alloy based composites”, Composites part-A 28, 301-309.
- S.F. Moustafa, (1995). “Wear and wear mechanism of Al-22%Si/Al2O3 composites”, Wear, 95, 185-198.
- D.P. Mondal, S. Das and A.K. Jha, (1998). “Abrasion wear of Al based composites, Wear, 223, 131-139.
- A.G. Wang and I.M. Hutchings, (1989). “Wear of alumina-fibre aluminum Composites”, Mater Sc. and Tech 5, 71-84.
- Wang and H.J. Rack, (1991). “Friction behavior of Al-SiCp composites”, Wear 146, 337-344
- M.A. Moore and R.M. Douthwaite, (1976). “Tribological behavior of ceramic based Composites”, Metall. Trans. 7, 1833-1842
- Joel Hemanth, (2005).“Tribological behavior of cryogenically treated Al-12%Si alloy/B4C composites”, Wear, Elsevier Science, 258 ,1732-1744.
- J. Zhang and A.T. Alpas, (1993). “Wear regimes and transition in Al2O3 particulate Composites”, Mater. Sc, and Engg. 161, 273-280.
- B. Venkataraman and G. Sundarajan, (1996). “The sliding wear behavior of Al-SiC particulate composites”, Acta Mater. 44, 451-462.
Citation: Joel Hemanth. (2019). Development, Characterization and Tribological Behavior of ASTM Grade Commercial Steel Reinforced with Tungsten Carbide (WC) Metallic Chilled Composites for Stone Crusher Jaw Application. Archives of Chemistry and Chemical Engineering 1(1).
Copyright: © 2019 Joel Hemanth. This is an open-access article distributed under the terms of the Creative Commons Attribution License, which permits unrestricted use, distribution, and reproduction in any medium, provided the original author and source are credited.